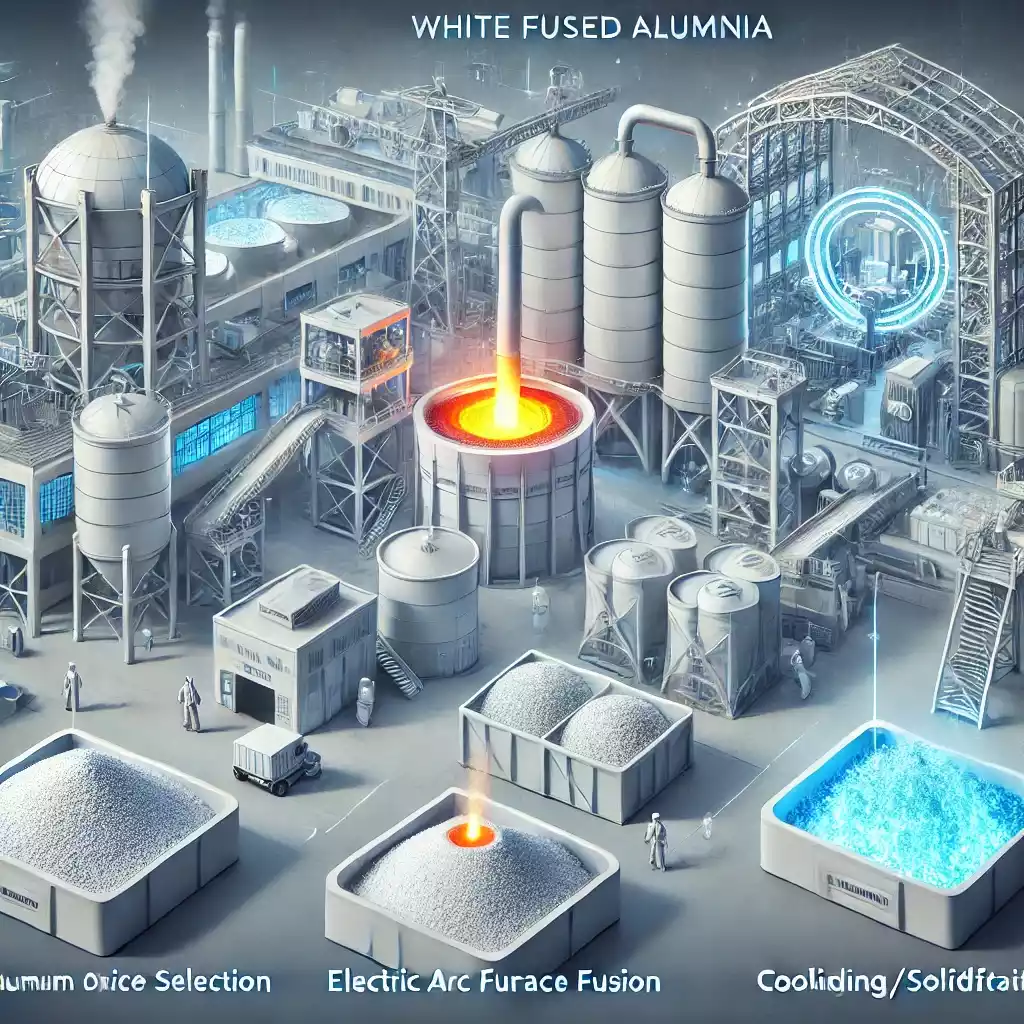
White Fused Alumina Manufacturing Process
The white fused alumina manufacturing process is crucial for producing a high-quality abrasive and refractory material known for its hardness, purity, and thermal stability. White fused alumina, made primarily from pure aluminum oxide (Al₂O₃), undergoes a complex production process involving high-temperature fusion, purification, and granulation. This article provides a step-by-step breakdown of the manufacturing process and insights into why it is a top choice for industries that demand strength and stability in extreme conditions.
What is White Fused Alumina?
White fused alumina, also called white corundum, is a premium form of aluminum oxide produced through an electric arc furnace process. The material’s high purity level, typically 99.7% Al₂O₃, contributes to its popularity in industries that require abrasion resistance, chemical stability, and thermal endurance. Due to its properties, white fused alumina is an ideal material for applications such as sandblasting, refractory products, and abrasive tools.
Honrel offers a comprehensive selection of high-quality abrasive and refractory materials, including white fused alumina, catering to industries worldwide.
The Step-by-Step Process of Manufacturing White Fused Alumina
1. Selection of High-Quality Aluminum Oxide
The process begins with selecting high-purity aluminum oxide, the raw material that ensures the quality and consistency of the final product. High-grade aluminum oxide with minimal impurities is preferred to achieve the white fused alumina’s high level of purity.
- Internal Link: For similar products, visit Chemical Raw Materials.
2. Electric Arc Furnace Fusion
The selected aluminum oxide is placed in an electric arc furnace and heated to extreme temperatures, typically above 2000°C. During this stage, the material undergoes a transformation, melting into a dense liquid. This high-temperature fusion helps eliminate impurities and produces a homogenous mixture of pure aluminum oxide crystals.
- Internal Link: Learn more about other refractory materials in Abrasive and Refractory Materials.
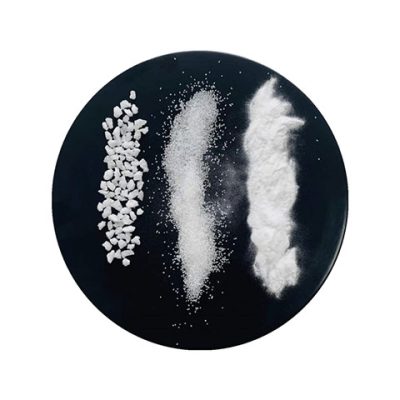
3. Cooling and Solidification
Once melted, the white fused alumina is cooled slowly to allow for controlled solidification. This stage forms dense and crystalline alpha alumina, which is resistant to wear and chemical degradation. The slow cooling process is essential for forming a high-purity product that meets industry standards.
4. Crushing and Grinding
The solidified alumina is then crushed and ground into specific grain sizes, depending on its intended use. For abrasive applications, fine particles are required, while larger grains are used in refractory applications for thermal insulation. This versatility in grain size allows white fused alumina to meet a wide range of industry needs.
- Internal Link: Explore Honrel’s White Fused Alumina for more information on available grain sizes.
Applications of White Fused Alumina
White fused alumina serves a wide range of industries that demand high-performance materials. Some of its primary applications include:
- Abrasives and Sandblasting: Its hardness makes it an ideal material for grinding wheels, cutting tools, and sandblasting.
- Refractory Products: Due to its thermal stability, it’s commonly used in furnaces and kilns.
- Ceramic Products: Its chemical resistance makes it suitable for ceramic production and spark plug insulators.
- Polishing and Finishing: The material’s purity and hardness are ideal for polishing applications in various industries.
For additional high-strength options, explore Tabular Alumina, another robust material provided by Honrel.
Key Factors Affecting the Quality of White Fused Alumina
The quality of white fused alumina can vary depending on several factors during the manufacturing process. Here are the primary considerations:
- Purity of Raw Material: Higher purity results in better performance for abrasive and refractory applications.
- Temperature Control: Proper temperature management during fusion ensures consistency.
- Controlled Cooling and Granulation: Controlled cooling prevents the formation of unwanted crystalline structures.
Comparing White Fused Alumina to Other Refractory Materials
Material | Key Properties | Applications |
---|---|---|
White Fused Alumina | High purity, hardness, thermal stability | Sandblasting, ceramics, refractories |
Tabular Alumina | High strength, low porosity | Refractories, ceramics |
Yttrium Oxide | High melting point, chemical stability | Specialty refractories, ceramics |
For industries seeking durable materials, Yttrium Oxide also provides an effective alternative with high thermal resistance and chemical stability.
Advantages of White Fused Alumina
- High Hardness: Suitable for abrasive applications like grinding and cutting tools.
- Thermal Stability: Performs well in high-temperature environments.
- Chemical Resistance: Withstands exposure to aggressive chemicals, extending its lifespan in industrial applications.
Honrel supplies white fused alumina and other chemical raw materials, making it easier for companies to source high-quality products in large quantities while saving time and costs.
Frequently Asked Questions (FAQ)
- What is white fused alumina made of?
- White fused alumina is made from pure aluminum oxide (Al₂O₃), which is fused at high temperatures.
- What are the main applications of white fused alumina?
- It’s used in abrasive tools, refractory products, ceramics, and sandblasting applications.
- How does the manufacturing process affect the quality of white fused alumina?
- The purity of raw materials, controlled fusion, and cooling processes ensure high quality and performance.
- What is the difference between white fused alumina and other types of alumina?
- White fused alumina is noted for its purity and hardness, making it more suitable for abrasives and high-temperature applications.
- Why choose Honrel for white fused alumina?
- Honrel offers high-quality, certified materials with competitive pricing and global distribution.
Analysis Tables
Table 1: Manufacturing Process Summary for White Fused Alumina
Stage | Description |
---|---|
Raw Material Selection | High-purity aluminum oxide selected |
Fusion | Melted in an electric arc furnace |
Cooling and Solidification | Slow cooling to achieve crystalline structure |
Crushing and Grinding | Granulated to desired grain sizes |
Table 2: Comparison of White Fused Alumina with Other Refractory Materials
Property | White Fused Alumina | Tabular Alumina | Yttrium Oxide |
---|---|---|---|
Melting Point | 2040°C | 2040°C | 2410°C |
Hardness | 9 Mohs | 9 Mohs | 6-7 Mohs |
Thermal Stability | Excellent | Excellent | High |
Common Applications | Abrasives, Refractories | Ceramics, Refractories | Specialty Ceramics |
Summary
The white fused alumina manufacturing process is an intricate procedure involving high-temperature fusion, controlled cooling, and granulation to create a high-purity material. Recognized for its hardness, thermal stability, and chemical resistance, white fused alumina serves critical roles in industries that demand durability and performance. Suppliers like Honrel deliver top-quality materials, supporting industries with bulk supply options and ensuring a consistent standard of quality across global markets.